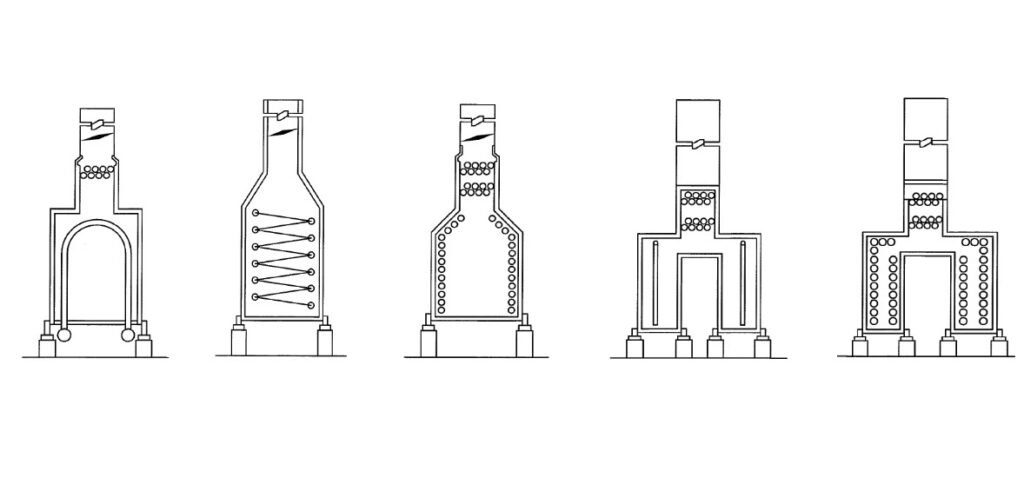
Introduction
API (American Petroleum Institute) style cabin heaters are essential equipment in various industrial applications, especially in the oil and gas industry. These heaters play a crucial role in maintaining optimal temperatures inside cabins, control rooms, and other critical areas, ensuring the safety and comfort of personnel. However, to ensure the safe and efficient operation of these heaters, it is essential to understand and implement proper equipment management safeties. In this blog post, we will delve into the key aspects of managing API style cabin heaters to guarantee their safe and reliable performance.
- Regular Inspection and Maintenance
One of the primary safety considerations when dealing with API style cabin heaters is regular inspection and maintenance. These heaters consist of complex components, including burners, heat exchangers, and control systems, which can deteriorate over time due to wear and tear. To prevent potential hazards, it is crucial to establish a routine inspection and maintenance schedule. Inspect and service the heater according to the manufacturer’s recommendations and industry standards. This will ensure that all components are in good working order and reduce the risk of accidents or malfunctions.
- Temperature and Pressure Monitoring
Temperature and pressure monitoring are critical aspects of managing API style cabin heaters. Cabin heaters operate under specific temperature and pressure ranges, and deviations from these parameters can lead to hazardous situations. Implementing temperature and pressure sensors with appropriate alarms is essential. These sensors can detect abnormalities and trigger alarms or automatic shut-off mechanisms when conditions become unsafe. Regularly calibrate and test these sensors to maintain their accuracy.
- Gas Detection Systems
Many API style cabin heaters utilize natural gas or propane as a fuel source. To manage these heaters safely, it is essential to implement gas detection systems. These systems can detect leaks or abnormal gas concentrations in the cabin area. If a gas leak is detected, the system can shut off the gas supply and activate ventilation to prevent the buildup of combustible gas concentrations. Routine maintenance and calibration of gas detection systems are crucial to ensure their effectiveness.
- Flame Monitoring
API style cabin heaters rely on flames for heat generation. Proper flame monitoring is essential to ensure the safe operation of these heaters. Flame sensors and scanners are used to detect the presence and stability of the flame. If the flame goes out or becomes unstable, the system should automatically shut down to prevent gas leakage and potential explosions. Regularly clean and inspect flame sensors to ensure their functionality.
- Emergency Shutdown Procedures
In the event of an emergency or malfunction, it is vital to have clear and well-documented shutdown procedures in place. Personnel should be trained on these procedures to react quickly and effectively in case of any issues with the API style cabin heater. Ensure that emergency shut-off switches and controls are easily accessible and clearly labeled.
Conclusion
Proper equipment management safeties are paramount when dealing with API style cabin heaters. These heaters are integral to maintaining safe and comfortable working environments in the oil and gas industry, but they also present potential risks if not managed correctly. Regular inspection and maintenance, temperature and pressure monitoring, gas detection systems, flame monitoring, and well-defined emergency shutdown procedures are essential components of ensuring the safe operation of these heaters. By prioritizing safety and implementing these measures, organizations can minimize the risks associated with API style cabin heaters and ensure the well-being of their personnel.
0 Comments